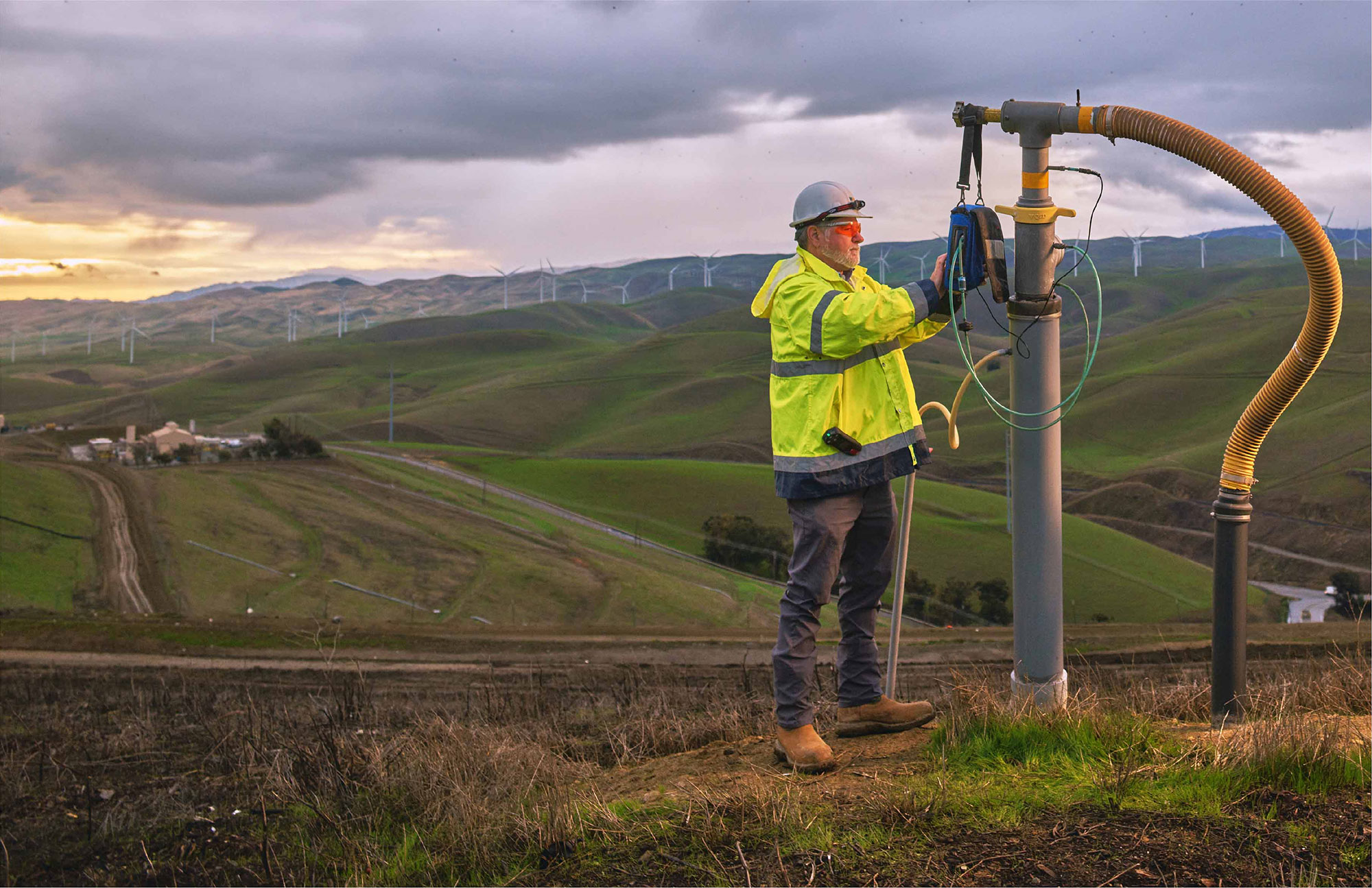
- Sustainability A-Z
- Environmental Management
Environmental Management
Environmental stewardship is the core of our business, our promise to customers, our competitive advantage and our obligation to the communities in which we operate. How we manage potential environmental impacts and opportunities is a critical element of being a sustainable enterprise. In a business as highly regulated as ours, protecting the environment, maintaining compliance and innovating to improve operations requires unwavering focus, expertise, comprehensive systems and internal checks and balances. Our approach has evolved over decades, with a focus on integrating environmental functions into key management systems.
Processes
We have a long track record of both supporting high regulatory standards and striving to go beyond them. Our environmental management approach has led us to undertake the following actions:
- Providing comments and technical guidance to federal, state, provincial and local agencies on the implementation of various environmental laws and regulations
- Innovating beyond compliance. As part of WM’s internal formal performance review, the results of regulatory inspections, internal audits, external audits, and regulatory compliance issues and their precursors are tracked, managed and remedied as part of the company’s continuous improvement process. Members of senior management, up to and including the Board of Directors, review performance.
- Extending the company’s commitment to environmental performance related to events that are not necessarily regulatory in nature but that, nonetheless, are public concerns, such as noise, litter and odors. Such events are tracked, managed and remedied. We also employ best management practices and conduct routine training to eliminate the dissemination of dust from our facilities.
- Testing our internal systems to ensure their thoroughness and accuracy. Periodically, we conduct gap analyses of our Environmental Management System against the International Organization for Standardization (ISO) 14001 standards to ensure the sufficiency of our systems for landfills, transfer stations, hauling operations, hazardous waste treatment and disposal facilities and recycling facilities. These systems continue to be evaluated and supplemented as appropriate.
- Offering environmental management services aligned with and certified under International Organization for Standardization (ISO) 14001 and ISO 9001 standards via WM’s Sustainability and Environmental Services (SES) team.
- Auditing our operations through an independent environmental audit team that employs nationally recommended compliance audit practices approved by the American Standards for Testing and Materials (ASTM) and the Board of Environmental, Health and Safety certification standards for professional auditors. Nearly all of WM revenues come from operations subject to environmental management systems that are audited.
- Testing our facilities to assure stakeholders that our operations protect human health and the environment. Our environmental experts hold a number of patents on innovative monitoring and analysis technologies, and we often provide monitoring data to outside parties to evaluate how our systems are performing.
Environmental Management System (EMS)
Our goal for environmental compliance is simple: sound environmental practices with zero deviations from regulatory standards. The goal of the EMS is to prevent conditions that could result in violations. If conditions that could result in violations occur, corrective and preventive actions are implemented as quickly as possible.
Our Corporate Environmental Policy establishes the vision for our EMS. The Policy states, in part, “WM is committed to protecting human health and the environment. This commitment is a keystone of all that we do, reflected in the services we provide to customers; the design, operation and long-term maintenance of our facilities; the conditions under which employees work; the implementation of our sustainability initiatives; and our interactions with the communities where we live and do business. We will be responsible stewards of the environment, leaders in sustainability, and will protect the health and well-being of our employees and neighbors. We will work to provide and create public awareness of the importance of environmental stewardship.”
The following principles are applicable to company operations worldwide:
- Protection: WM conducts operations in a manner that protects the environment and WM employees, neighbors and customers. We proactively work to identify and manage risks to prevent pollution, reduce emissions and releases, and prevent or reduce other possible adverse consequences from our operations.
- Compliance: WM strives to comply with all environmental laws and regulations and proactively implement programs and procedures to ensure compliance and promote environmental responsibility.
- Sustainability: At WM, we practice and promote sustainability through the conservation of nature and the earth’s energy resources and the reuse and recycling of materials that otherwise are wasted.
- Communication: All WM employees are responsible for helping the company identify potential threats to human health and the environment from our operations and remedy possible non-compliance with environmental laws and regulations. Suspicion of violations of law or WM’s Core Values of Ethical Conduct and Practices shall be communicated in accordance with the company’s Business Ethics and Compliance Policy and Environmental Reporting and Incident Notification Policy.
- Disclosure: WM provides annual updates on its environmental goals and key indicators and provides a comprehensive sustainability report annually.
- Engagement: WM seeks opportunities to engage with stakeholders on environmental, social and governance issues, and reports on the groups with which we engage.
The company has developed processes, procedures and tools for use in achieving its high standards for environmental performance and compliance. The company’s operations, across all lines of business, are responsible for implementation and adherence to the EMS at each operating location. This applies to all business endeavors in which WM has 50% or more ownership.
Our management will regularly monitor operations and make recommendations to the Board of Directors on programs to continuously improve the environmental performance of the company. Environmental goals and objectives will be established, reviewed and approved during management review. The WM Board of Directors and executive management will regularly monitor environmental performance to ensure adherence to the principles of this policy across the company.
Our EMS focuses on preventing, correcting and ultimately reducing impacts associated with our operational activities. Specifically, we focus on eliminating:
- Environmental impacts which include spills or leaks from vehicles, landfill gas impacts on the air or subsurface and releases to surface water or groundwater
- Community impacts including odors, litter, noise, dust and spills or leaks
- Regulatory impacts such as regulatory inspection-alleged issues, warning letters, violations and enforcement actions
We also use several databases, systems and processes designed to help facility managers plan, implement, check and respond to their site-specific environmental requirements.
Objectives and Targets
We use indicators to quantify environmental performance, including environmental impacts, community environmental concerns and impacts and regulatory violations. Our Environmental Incident Rate (EIR) measures our performance and tracks progress toward these goals at the facility level. The EIR is used to drive continuous environmental improvement on a year-over-year basis.
Roles and Responsibilities
Our EMS relies on our corporate, geographic area and facility-level personnel with job-specific functions, roles and responsibilities for planning, implementing and evaluating the EMS components. The specific departments and personnel involved include the following:
- Environmental Protection (EP) develops environmental policies, tools and training, and provides strategic or technical advice, with the goal of 100% compliance. The team oversees environmental performance and ensures environmental impacts and issues are resolved, including correction and prevention.
- Environmental Management Team provides expertise in the planning and design of our facilities to ensure that operational activities have limited environmental impact. They manage research and engineering science to develop an understanding of the interrelationships between our disposal processes and the environment. The team provides expertise and direction on air, land and water protection programs and ensures that environmental monitoring networks are installed and operating to specifications.
- Site Managers and Frontline Employees are responsible for all environmental aspects at the site level, with key environmental tasks assigned to appropriately trained local staff.
Training
WM recognizes that to achieve environmental performance goals, employees must possess the knowledge and skills to manage and conduct operations in environmentally responsible ways. Our environmental training targets a range of operational and functional levels within the company. All new employees participate in corporate ethics and compliance training, which includes our company’s standards for environmental practices. Corporate and local staff with responsibility for environmental leadership are trained in the company’s environmental practices. Employees with environmental leadership responsibility, such as facility managers and environmental and compliance technical staff, are provided training through both online learning modules and on-site trainings conducted by our field EP and/or operations professionals. The Environmental Protection Learning Series (EPLS), available through WM’s learning portal, is a monthly series covering site management trainings featuring a different environmental subject each month.
In addition, WM has environmental training programs targeting operational and functional levels. Our Environmental Compliance Awareness Program provides mandatory monthly training for frontline employees and managers, covering a different environmental subject each month. Knowledge is tested and tracked at the site level.
Local training is also provided periodically via in-house classroom training, on-the-job training and outsourced training.
Communications
Communicating environmental commitment and performance to our customers, communities, regulators and investors strengthens our ability to be an environmental leader in our industry. Internal communications regarding environmental commitment and performance help create an atmosphere where all employees work toward the common goal of continuous improvement.
We communicate our environmental commitment within the company using the following methods:
- WM’s Environmental Incident Notification Policy gives immediate, company-wide notification of significant environmental or regulatory events — including reportable quantity (RQ) spills, environmental impacts (e.g., stormwater leachate), alleged violations and enforcement actions
- WM’s Public Commenter Systems provide real-time notification of customer-related environmental issues to site managers for response and resolution
- Environmental performance results are tracked monthly via the Environmental Protection (EP) Dashboard and communicated to senior leadership
We have a wide range of environmental databases including the following:
- Environmental Health & Safety (EHS) Portal Permits & Task Management: The compliance assurance task calendar program for identifying and tracking the completion of site environmental tasks regarding permits, regulations, site plans, policies, etc.
- EHS Portal Environmental Reporting System (incident alerts): The repository for reported agency-identified violations (AIVs), environmental exceedances, self-identified concerns and public comments. Corrective and preventive actions are also tracked through this process
- Storage Tank Database: Used to manage aboveground and underground storage tanks, including registrations for insurance purposes
- Applied Landfill Information Analysis System (ALIAS): A relational database used to cross-reference landfill characteristics (e.g., cover, liner, waste type) to monitoring points and results
- EQuIS: Contains our groundwater, surface water and other analytical data provided by contract laboratories. Used for reporting, data integrity and management purposes
- Landfill Gas Management System (LGMS): Houses operational and performance data relating to landfill gas collection and control systems
In addition to the above, each facility is responsible for maintaining its own operating record, including documents, inspections and reports required by regulation.
Emergency Preparedness and Response
We’re always working to refine and improve the disaster response and preparation plans for our facilities. We maintain an Emergency Situations and Evacuation Plan Policy, which communicates management objectives for addressing emergency situations. Facilities may also be required to maintain specific emergency response plans, including the following:
- Hurricane Preparedness Plans and annual simulation exercises
- Disaster Preparedness and Management Plans in areas subject to natural disasters (e.g., tornados, fires, earthquakes), for safe handling of disaster-generated debris
- Spill Prevention Control and Countermeasures (SPCC) Plans for facilities that store certain volumes of petroleum products and are required to prevent, contain and control spills
Our employees are trained and drilled to comply fully with Emergency Situations and Evacuation Plans, Local Preparedness Plans and Spill Plans.
Monitoring and Measurement
We use the following programs within our EP Dashboard as a multipurpose, integrated system to monitor, measure, report and track environmental aspects and impacts through closure/completion:
- Environmental Incidence Rate (EIR):This online system is used to measure, track and report performance across three areas: the environment, our communities and regulations. Our performance goal is continuous year-over-year improvement in EIR performance.
- Environment: We compile environmental incidents that occur at our operations, including the following:
- Groundwater impacts that exceed regulatory criteria or that show increasing trends
- Stormwater impacts above reportable release levels
- Air impacts that include reportable air emissions
- Landfill gas impacts registered by perimeter gas probes
- Community: To underscore the company’s commitment to the communities it serves, WM developed and deploys a public comment management system. When a comment is received, the information necessary for a prompt response and remedy is routed to the closest responsible manager. The manager is empowered to take action, appropriate to the circumstances, and track remedies through to completion.
- Regulatory: Regulatory incidents and, more importantly, their precursors are tracked, managed and recorded for each occurrence as part of the company’s compliance program and continuous improvement process. Lessons learned are shared via the company’s EP Dashboard and program of weekly and monthly reporting. Senior management, including the Board of Directors, is briefed on performance on a regular basis. The position of Chief Compliance Officer exists to elevate the issue of regulatory compliance.
- Environment: We compile environmental incidents that occur at our operations, including the following:
Corrective Action and Preventive Measures
Local EP Managers are responsible for ensuring resolution and prevention of issues identified through the EP Dashboard, EP Toolkit and other environmental database reports. Facility and EP Managers are responsible for ensuring that identified incidents are closed out completely and correctly. Measures or actions that are not effective are subject to reopening of the incident.
- EIR incidents are documented and tracked until corrective actions and preventive measures are implemented. Performance related to completion of the corrective and preventive measures is tracked via the EP Toolkit.
- The public comment management program is the process for addressing environment-related calls from our customers and communities. Any comment requiring corrective action is routed to the local entity for response and resolution. Environment-related comments are centrally tracked through correction and preventive measure implementation.
- The WM Integrity Helpline is our portal to internally identify potential instances of noncompliance with company or regulatory procedures. We communicate its availability for use to employees and promote a Speak Up culture — when they speak up, we listen up and follow up. Every inquiry is logged and tracked to ensure that the issue is resolved, up to and including any required corrective actions. The Legal department and EP work together to assess whether the incident has any national implications and to ensure that a lesson learned in one location is rippled across the organization. The Helpline is maintained by a third party where reports can be made anonymously 24 hours a day, seven days a week.
Our facilities are expected to ensure that corrective actions and preventive measures are effective. Environmental issues are not closed out in any of these systems without the concurrence of the EP Manager.
Compliance Audits
WM’s Corporate Compliance Audit Services (CAS) conducts independent EHS and transportation compliance audits. Each year, the department conducts hundreds of audits at facilities owned, operated or controlled by the company. Audit planning and scope are based on risk assessment principles, including the nature of operations and consideration of emerging regulatory and EHS trends. CAS reports to the Chief Compliance and Ethics Officer and the Board of Directors. Audit practices are in accordance with nationally recommended compliance audit practices approved by the ASTM (2000) and the International Internal Audit Standards Board’s (IIASB) International Standards for the Professional Practice of Internal Auditing (2017).
CAS evaluates and supports improvement of the company’s EHS performance through the following activities:
- Conducting systematic, documented and objective evaluations to verify compliance with environmental regulatory requirements
- Assisting the company in evaluating and improving the effectiveness of existing EHS and transportation systems and policies
- Assisting the company and its managers in preventing, detecting, correcting and proactively addressing compliance issues
CAS processes and procedures include the following:
- Assessing risk and selecting facilities to audit
- Training of staff conducting audits
- Developing audit protocol documents
- Planning and conducting audits
- Identifying noncompliant activities
- Resolving audit findings
- Documenting management and retention
- Reviewing and updating program directives and procedures
- Auditing quality control and assurance
- Communicating audit results
Facility staff use designated programs to document resolution of audit findings. CAS reviews findings before they are closed and conducts verification audits to ensure that the finding resolution was effective. CAS communicates the audit results to relevant local and corporate management and follows up to ensure the timely resolution of issues identified through its compliance audits.
As part of our auditing and compliance process, we ensure that we can monitor the final destination of our waste, that no hazardous waste is transported from developed countries to developing countries, and that products sent from developed countries to developing countries for repair or resale are not waste. WM’s electronics recycling division is Sustainable Electronics Reuse & Recycling (R2) Standard v3 (R2V3), ISO 9001:2015, ISO 14001:2015 and RIOS:2016 certified.
The Sustainable Electronics Reuse & Recycling (R2) Standard requires certified organizations to comply with all applicable import and export laws covering shipments of Focus Materials generated from the processing of electronics in accordance with the Basel Convention and with Section 6 (1) of the Standard for Reusable Equipment and Components, Tested and Full Function, R2/Ready for Reuse requirements.
WM’s electronics recycling division is audited regularly for compliance with the standards to which it subscribes; this includes monitoring of final destinations for destruction, recycling, refurbishment, reconditioning and/or resale.
Records
Certain data elements are reported with routine frequency, while others are reported on a non-specified schedule. For details on environmental impacts please see the Non-Compliance Associated with Environmental Impacts section of the Sustainability Data Center.
Certain groundwater and surface water test data are collected on a routine basis and tied to sampling events specified in operating permits, licenses and applicable permits (usually quarterly or semiannually). These results are housed centrally through our laboratory management program and are reported as they are generated.
Records relating to analytical results, environmental performance elements and compliance assurance tasks are maintained online within our IT, Legal and/or Environmental Protection departments. Documents and technical resources are available and maintained on our Visor and SharePoint intranet sites, as are training, guidance and standards resources.
Our facilities must annually certify their compliance with applicable permits and regulatory requirements through our centralized Compliance Representation Letter process, which is reviewed by senior management.
Our management teams participate in a management review process to determine the level of success in achieving environmental goals. In doing so, they complete the following tasks:
- Review environmental policies
- Review WM’s EMS
- Routinely monitor and review environmental performance, issues and incidents on the EP Dashboard
- Evaluate corporate and local environmental goals and objectives
- Amend the EMS as needed, including policies, procedures, goals and objectives
Management review and response to environmental performance measures, incidents and issues are used to drive operational changes and ensure that continuous improvement goals are met. Our Internal Audit department performs compliance evaluations on an ongoing basis.